So-called “generative design studio” Nervous System designed a dress that could be fabricated entirely by a 3D printer—in one shot, with no assembly required afterwards—it emerges as a completed, ready-to-wear garment. The studio refers to the process as “kinematics,” and the dress is actually an intricate network of very small hinges that allows it to flow in a cloth-like manner, almost completely sidestepping the rigid forms that one would normally expect to emerge from a 3D printer. Nervous System worked with Shapeways to do the fabrication, which took 44 hours, and described their process in this interview. An excerpt:
Kinematics represents a new approach to manufacturing, which tightly integrates design, simulation, and digital fabrication to create complex, customized products. Our approach is completely different from traditional modeling and CAD software. The whole system is built up around the logic of a mechanism, in this case a hinge, which has been optimized for 3D printing and whose behavior we can simulate. Users interact with kinematics at a high level through an online design tool that lets them sculpt clothing shapes and ‘paint on’ density and styles. Meanwhile, in the background the system is taking care of generating and connecting together all the geometry with our hinge mechanism. At the end of the design process, we have a 3D-printable piece of clothing made of thousands of panels interconnected by hinges. Rather than just ending up with big heavy file containing a bunch of ‘dumb’ geometry, we end up with a smart structure that we understand as rigid panels connected by hinges. Because we understand the behavior of the geometry, we can use simulation to compress it down for efficient 3D printing.
All that technical accomplishment aside, the dress is actually quite beautiful.
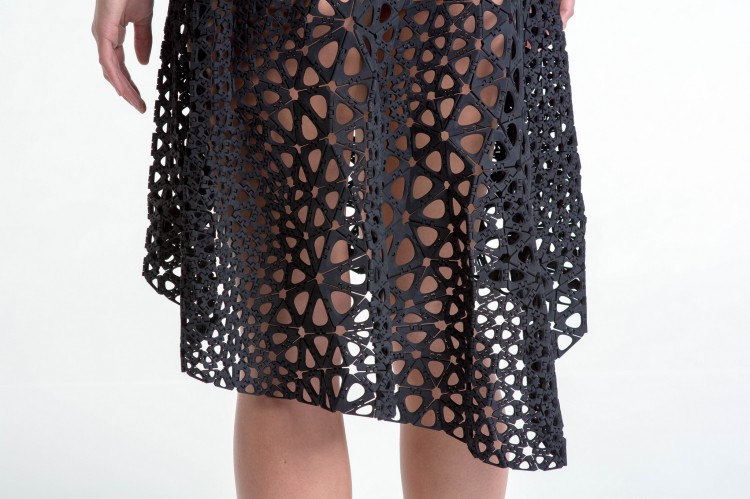
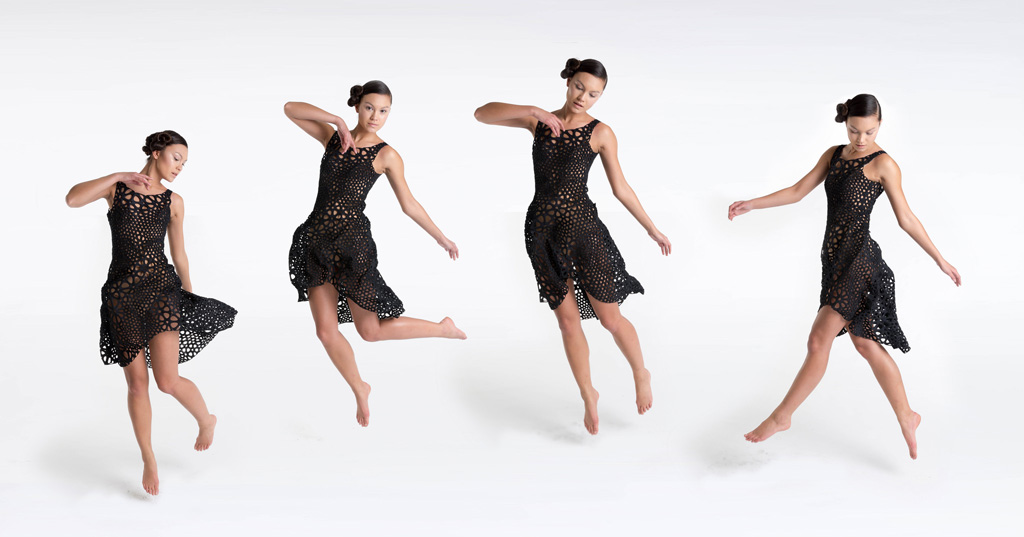
Read more at shapeways.com and at n-e-r-v-o-u-s.com.
+